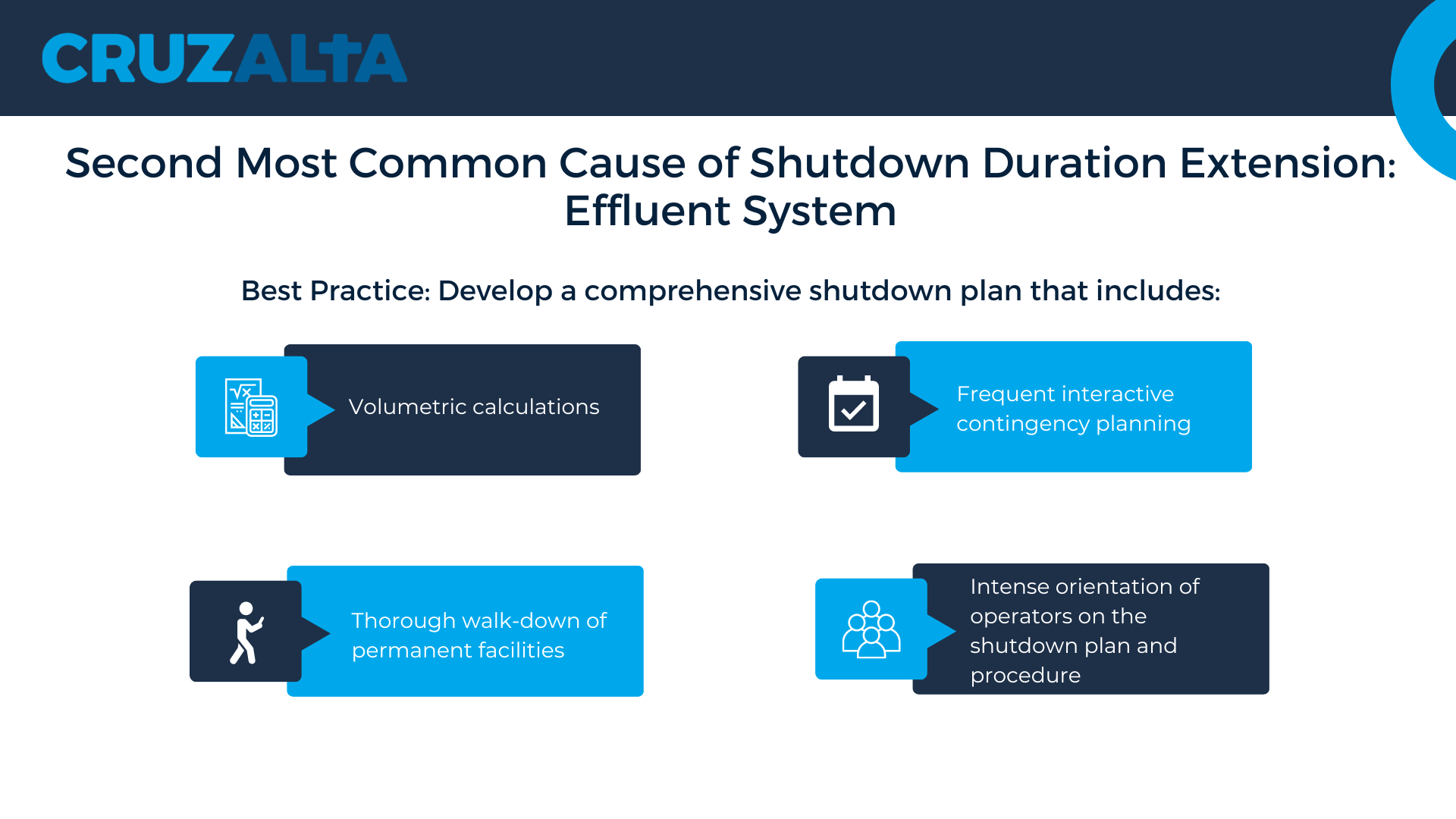
Effluent Management
In our previous blog, we introduced the top four turnaround delays and more deeply explored the #1 cause, mechanical readiness.
Now we will discuss the #2 cause: effluent management.
Effluent management includes any deficiency associated with the facilities being used for handling the liquid effluent created during the shutdown steps. The most frequent scenario is when the system is hydraulically limited, which is typically the result of undersized temporary piping, a decision to not use temporary facilities to increase the capacity of permanent piping, effluent system overload due to unit sequencing changes, or inadequate system design (such as not installing temporary coolers or pumps). Occasionally, equipment failures and the presence of unplanned orifice plates occur, which fall within this category.
A best practice for effluent management is to develop a comprehensive shutdown plan that includes volumetric calculations, thorough walk-down of permanent facilities, frequent interactive contingency planning, and intense orientation of operators on the shutdown plan and procedure.
Turnaround delays are a common issue, but they don't have to be. As a means of helping mitigate those delays, we want to provide you with proactive options. If you are experiencing any of these turnaround setbacks, let us know. We’re here to provide you with solutions.
RELATED ARTICLES
Top 4 Causes of Turnaround Delays
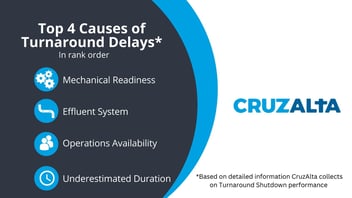
Turnaround failures are an unfortunate fact of life for many refineries, and no one wants to...
Underestimated Duration
Underestimated Duration is the fourth most common cause of shutdown timeline extension. Unlike the...
READ MORE →A Craftsman Toolbox: CruzAlta's Turnaround Management Consulting
.png?width=352&name=CAPE%20%20(1).png)
CruzAlta’s Turnaround (TA) Management consulting program is quickly gaining industry attention...
READ MORE →
LEAVE YOUR COMMENT